ビジネスシーンでよく聞くキーワードのひとつである「ボトルネック」。ボトルネックとはどんな概念なのか。ボトルネックが発生する要因や改善するためのプロセス、生産性を高めるためにボトルネックと向き合うポイントについて、日本総合研究所の吉田賢哉さんが解説します。
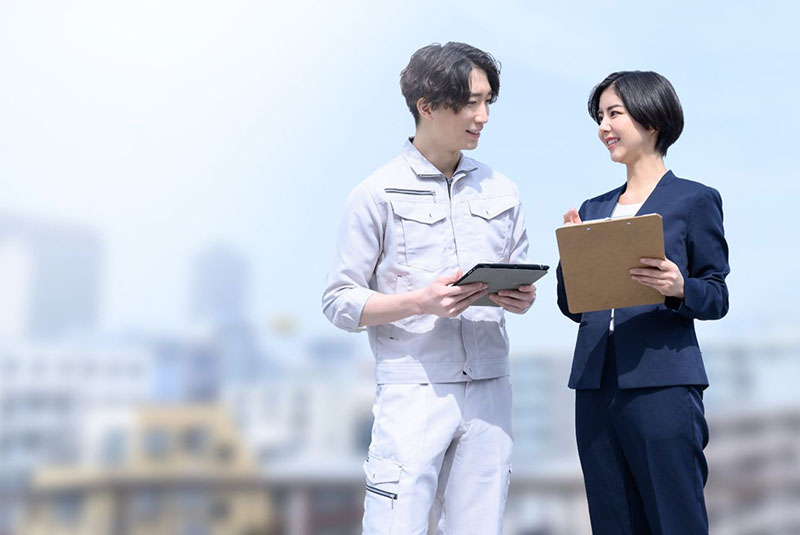
ボトルネックとは、相対的に弱いところ
ボトルネックとは、「bottleneck」をカタカナ表記したもの。その言葉通り、「瓶(ボトル)の首」を意味します。ビジネスシーンにおいては、全体の中で相対的に弱いところ、弱点を指します。
なぜ、瓶の首が「相対的に弱いところ」を意味するかといえば、他の部分に比べて細くなっていて、流れが詰まりやすいからだと言われています。ビジネス現場においても、スムーズな流れが滞る部分、ほかに比べて弱いところを指して、「あそこがボトルネックだね」などと使われることがあります。
例えば、食品メーカーの冷凍食品工場の生産ラインは、「材料を切る」「炒める」「盛り付ける」「包装する」など複数の作業があり、それらがすべてスムーズに連携することで、製品のモノづくりは成り立っています。
ところが、包装する機械に何らかの不具合が生じれば、そこまでの工程がどんなに順調だったとしても、完成品はできません。その場合、包装ラインが「ボトルネックになっている」ということになります。
ボトルネックが発生する要因・背景
どんなにうまくいっている事業においても“相対的に”弱い部分、つまりボトルネックは何かしらあると言えます。ビジネスは、様々な要素の組み合わせで成り立っているからです。
続いては、「本棚を生産する工場」の工程を例にしながら、ボトルネックが発生する要因や特敵の仕方などを、さらに具体的に説明していきます。
その工場には、「1時間で本棚100個分の材料を切断することができる工程」「1時間で本棚120個分の塗装に対応できる工程」「1時間で本棚80個分の組み立てを行える工程」「1時間で本棚150個分の出荷前検査が実施できる工程」があったとします。
この場合、「この本棚工場が1時間で作ることのできる本棚は80個」になります。一番弱い組み立て工程がボトルネックとなり、1時間に80個しか対応できないからです。
既定のサイズにカットされ、塗装も済んだ材料の在庫が、組み立て工程の前にどんなにたくさん用意されていたとしても、組み立て工程の見直しを図らない限り、1時間当たり80個までしか生産できないことは変わりません。
モノづくりのみならず、システム開発やコンシューマー向けサービスを行うビジネスにおいても、購買・調達部門、生産・開発部門、営業・販売・マーケティング部門、管理部門などさまざまな役割の組み合わせで成り立っています。この中の相対的に弱いところがボトルネックとなり、ある会社のビジネス活動に上限を設けてしまいます。
本棚工場内のボトルネックが強化され、たとえ工場で1日2,000個生産できる体制が整っていたとしても、販売店が1日1,000個しか売ることができなければ、今度は販売店がボトルネックとなり、本棚の在庫が積み上がることになってしまうでしょう。
事業を構成するさまざまな要素がある以上、どうしても「相対的に弱いところ」は生まれてしまうのです。
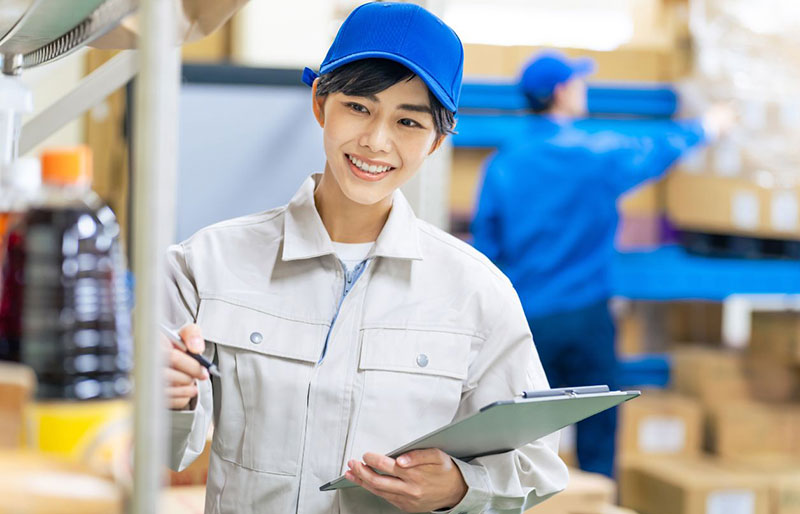
ボトルネックとなる「弱い点」を特定し、改善するプロセスと対策
とはいえ、事業の成長を目指すのであれば、ボトルネックを解消する対策は欠かせません。そのためには、そもそもボトルネックがどこにあるのか(一番弱いところはどこか)を特定することからスタートする必要があります。
ボトルネックの特定
先ほどの本棚の例で考えてみましょう。組み立て工程が弱いことに気づくことができれば、以下のような対策を立てることができます。
・組み立て工程に対応する人数を増やす
・組み立て工程の作業効率化に役立つ機械を導入する
上記のように人員増加や機械の導入などの対策により、組み立て工程の対応力を強化すれば、工場全体における本棚の1時間当たりの生産量を増やすことができるでしょう。
新たなボトルネックへの対応
すると今度は、組み立て工程がボトルネックではなく、材料を切る工程が新たな工程がボトルネックとなります。
例えば、1時間当たり本棚140個の組み立てが可能になれば、今度は、材料を切る工程が1時間に100個分までしか対応できないことが新たなボトルネックになり、工場全体における本棚の1時間当たりの生産量は100個になります。
ボトルネックの特定・強化を繰り返す
このようにビジネスの現場においては、常に「相対的に弱いところ」であるボトルネックを探し、改善策を考えていく繰り返しが重要になります。しかし、ボトルネックの特定を誤ると、事業全体にマイナスの影響を及ぼすこともあります。
ビジネスにおける難題の一つが、この「ボトルネックを探すこと」です。上記の例でいえば、本来の弱点である組み立て工程を改善せず、材料の調達や加工の工程を強化してしまうと、組み立て前の在庫が増え、在庫管理のコストが増大します。
しかしこの本棚の例のように、時間当たりの処理量が明確に分かるケースのほうが少ないかもしれません。どこを改善すればより売上が上がり、事業成長につながるのか。ボトルネックを突き止めるための分析力が、企業の強さを支えるともいえるでしょう。
「バランスの良さ」を意識することでボトルネックを緩和
ボトルネックはどんな企業にも存在しているものです。そして、「ビジネス活動のバランスの良さ」を意識することで、ボトルネックの負の影響を緩和することができます。
例えば、製品の機能が優れており、品質へのこだわりが強い昔ながらのモノづくり企業があったとします。しかし、近年の消費者が商品を選ぶ際には、デザインやブランドイメージなどが重要な要素となるため、過剰に品質にこだわりすぎてしまい、結果、ボトルネックが解消されず、売上増・ビジネス上の成功につながらないケースとなることもあります。
徹底的に品質にこだわる企業姿勢は称賛されるべきものではありますが、デザインや販売・マーケティングなどに一定の資金や人員を投入した方が、結果的に売上や利益の増加につながるケースは少なくありません。
ビジネスは、機能や品質のみならず、デザインやブランドイメージも含めて成り立っているというバランス感覚・多角的な視点による分析が伴わないと、結果としてボトルネックになっているデザインやブランドイメージが改善されず、売上増・ビジネス上の成功を実現することができません。
ボトルネックを見つけ出し、改善を図るには、様々な要素がボトルネックとなる可能性を疑い、幅広い多角的な視点でビジネス活動を俯瞰し、バランス良くビジネス全体を伸ばそうとする発想が必要だと言えます。
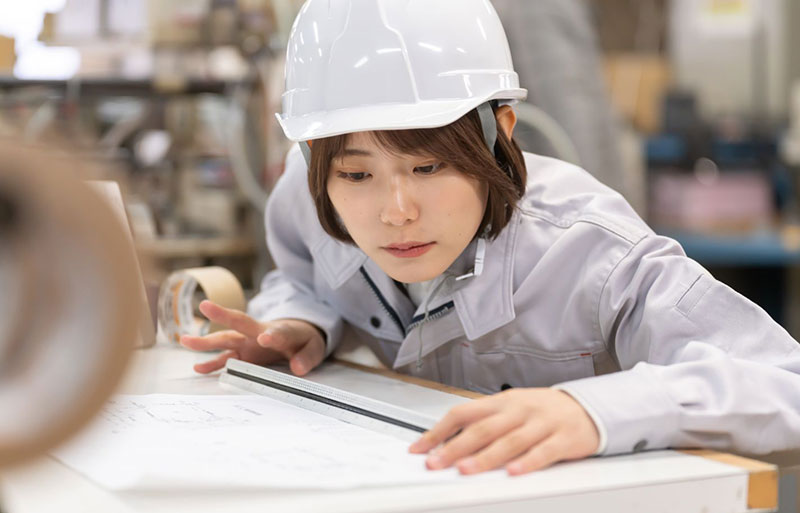
モノづくりの工場を改めて考えると、特定の工程だけ強くしても全体の生産量は増加しません。各工程の担当者がそれぞれ生産性を上げることは大切ですが、各工程を組み合せて全体像を見る責任者を置くことも重要です。
全体最適を意識しながら課題を捉え、改善策を考えることが重要であると強く認識することは、モノづくりにおいてバランスの良さを意識する第一歩と言えるでしょう。
さらに、ボトルネックの解消には、ビジネス活動全体をより幅広く捉える視点が重要になります。
良い製品を作ることができても、うまく売ることができなければ、ビジネス全体が順調とは言えません。デザインやブランドイメージ、販売・マーケティング、物流、アフターサービスなど、幅広いビジネスの構成要素に気を配りながら、ボトルネックを見つけ出し、その改善にどこまで投資するかを考えていくことが重要です。
モノづくりにおいても、経営・ビジネス全般においても、ボトルネックと向き合うには、バランス感覚を持って自身の事業を眺め、相対的に弱いところを見つけ出し、その強化に取り組む判断を下していくことが求められます。
▶あなたの知らない自分を発見できる。無料自己分析ツール「グッドポイント診断」
株式会社日本総合研究所
リサーチ・コンサルティング部門 シニアマネジャー 吉田賢哉氏
東京工業大学大学院社会理工学研究科修士課程修了後、日本総合研究所に入社。新規事業やマーケティング、組織活性化など企業の成長や、産業振興・地域振興・地方創生などを幅広く支援。従来の業界の区分が曖昧になり、変化が激しい時代の中で、ビジネスの今と将来を読むために、さまざまな業界のビジネスチャンス・トレンドについて多角的・横断的な分析を実施。